Inventory You Can Control - Down to the Bin
Organize stock, automate replenishment, and track every item across location.
When your inventory is spread across warehouses, vendors, and product lines, visibility isn’t enough—you need control. Acumatica gives you the tools to manage every piece, from shelf life and bin location to reorders and kits, so nothing gets lost, delayed, or overstocked.
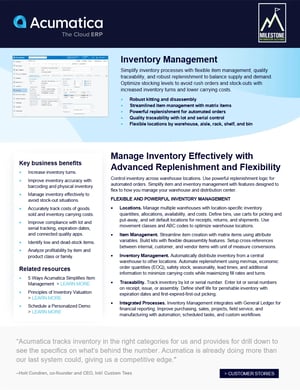
Streamline Movement, Minimize Waste, and Make Better Inventory Decisions
Manual processes and disconnected systems lead to overstocked shelves, stockouts, and costly delays. Acumatica brings everything together—from replenishment rules and warehouse locations to lot tracking and item kits—so your team can stay efficient, accurate, and always a step ahead.
Automate Replenishment with Precision
Use min/max levels, lead times, safety stock, and seasonality to trigger smart reorders.
Organize Inventory by Location
Manage stock by warehouse, aisle, rack, shelf, and bin—down to the most specific level.
Track Lots, Serials, and Expirations
Improve traceability and compliance with full visibility into perishable or regulated items.
Streamline Kitting and Disassembly
Build and break down kits with flexible tools that adjust inventory in real time.
Simplify Complex Item Management
Use matrix items to manage variations like size, color, or model—all from a single screen.
Spot Dead Stock Before it Piles Up
Use dashboards and inquiries to identify slow-moving items and optimize storage space.
Take Control of Your Inventory From End to End
Download the datasheet to see how Acumatica helps you automate reorders, track inventory by location, and eliminate stock issues before they start.